Designing the factory of tomorrow
Thursday, July 20, 2023
Media Contact: Stephen Howard | Manager of Communications | 405-744-4363 | stephen.howard@okstate.edu
Nobel Prize-winning physicist Dennis Gabor famously said the best way to predict the future is to create it.
That’s precisely what a collaborative team of researchers — engineers, computer scientists and behavioral scientists — from Oklahoma State University and across the nation plan to do for the world of manufacturing.
Led by Spears School of Business professor of management Dr. Bryan Edwards, the OSU team is purposefully designing the factory of tomorrow, which will weave artificial intelligence (AI), automation and humans seamlessly together in a manufacturing ecosystem that takes productivity and safety to the next level while opening the door of skilled labor to people that could only dream of it today.
“Let’s create the jobs of the future instead of letting them just happen haphazardly,” Edwards said. “Let’s get ahead of it. Let’s envision the factory of tomorrow.”
Edwards has assembled a team of OSU researchers that includes Dr. Dursun Delen, a Regents Professor of Management Science and Information Systems (MSIS) at Spears Business and the Director of Research for the OSU Center for Health Systems Innovation; Dr. Weihua Sheng, an electrical and computer engineering professor at OSU’s College of Engineering, Architecture and Technology; and associate professor Dr. Christopher Crick of the OSU Department of Computer Science, who has worked extensively with models of human cognition and social development to improve robot control and learning, human-robot interaction and artificial intelligence in general.
The OSU group has joined faculty from the University of Louisville, the University of Kentucky, the University of Texas-Arlington and Cornell University to submit grant proposals that have the potential to change the world of manufacturing.
The ambitious project aims to revolutionize the way workers and manufacturing centers interact, and would include everything from the walls of the factory to the skin of the employee. Much of it involves collaborative interfaces that help people work alongside robots in intuitive and groundbreaking ways. The public is already aware of some collaborative interfaces like virtual reality headsets, but they can also include wearables such as haptic-capable clothing that can detect pressure, heat and vibration. With technology like this, a worker could grab a robot’s arm, which has a sleeve of pressure sensors, and teach it a motion thanks to onboard AI programs that have the power to understand human intentions.
“We can use AI so that the robot understands our intentions based on body language, what we’re doing, our movements, and then we can communicate our intentions to that robot, and they’ll almost immediately pick it up,” Edwards said. “Think about using robots to lift heavy objects instead of humans. You notice something’s tipping over and the robot senses it too, immediately. Think about being able to communicate to a robot as you’re lifting heavy objects and going through a door. That involves twists and turns, and it will have to understand what you’re asking it to do.”
This technology would substantially increase the speed of production. Things that previously took years to develop, such as the research and design of a new vehicle, could be done in the blink of an eye thanks to AI software that can instantly reference the designs of every vehicle ever made, as well as the latest in safety innovations and consumer habits. Then, workers and automated machines could fit the parts together in a collaborative and safe environment.
It has the potential to open new opportunities to underemployed people across the world. The passage of the Americans with Disabilities Act in 1990 helped many people enter the workforce, but those with disabilities are still unemployed and underemployed at staggering rates. In Edwards’ opinion, collaborative interfaces can be the key to creating opportunities for those that didn’t have them before. Robotics and AI working in conjunction with collaborative interfaces could help level the playing field for those with debilitating injuries, older workers and less-skilled workers.
Delen, who has spent 30 years in data science and AI machine learning on top of his work with the Department of Defense and NASA, believes the increase in efficiency afforded by new technology could also bring outsourced manufacturing jobs back to the United States.
“People think AI and machines are going to take over the work,” Delen said. “But that is not going to be the optimal way to pursue it. It should be an augmentation, a mixed initiative, an optimal combination of humans and robots and AI working together. And when that happens, manufacturing that has been offshored, outsourced to other countries, will come back to the U.S. because it's going to be cost-efficient and it's going to be streamlined in a way that humans and robots will work together at a significantly higher level of efficiency.”
Getting people to understand the benefits of the factory of tomorrow may be the first step, but the second and possibly most important step will be getting people to trust it. Throughout history, humans have shown a level of resistance to new tools and technology, and Edwards, a behavioral scientist, sees it happening now with AI.
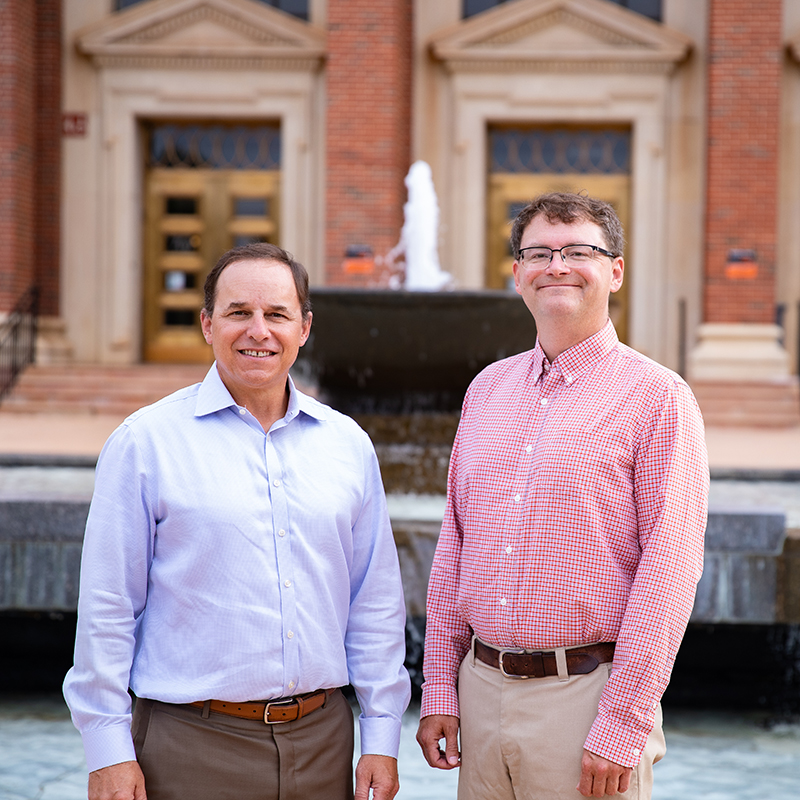
He said research shows that illustrating AI’s strengths will only go so far in persuading people to use it, and he points to self-driving vehicles as the prime example. Edwards has personally conducted research on driving performance with the Texas Transportation Institute in College Station, Texas. His research looked at data on accidents, accident avoidance, road-rage incidents, driving performance and everything in between. The results were clear.
“Humans should not be driving at all,” Edwards said. “We’re terrible at it, but we all think we’re going to be better drivers than that self-driving car. And that speaks to how hard it will be to get people to incorporate AI technology into their lives.”
Edwards said that communicating how AI will benefit each individual person will be the key to acceptance, and that starts with the next generation. His plan is to create a master’s degree geared toward the science of future technologies in the workplace. People in these positions will not only envision the future of industries, but will also work with grade schools across the country to help implement the skills that will be needed when today’s kids enter the workforce.
This will help dissuade fears that new technologies are here to take jobs from people – another key in getting the workforce to trust AI and robots. Rather than entering the job market with fear, the next generation will be prepared to work alongside technology and adapt to it as it changes.
“Throughout human history, new technology has replaced human jobs, but we’ve always maintained a pretty steady employment rate,” Edwards said. “In other words, there are other jobs that the new technology creates, even if it replaces some of the existing jobs. So, being able to get out in front of that and identify the new jobs that will be created will be another measure of success for us.”
In 2020, Edwards and Dr. William Paiva, executive director of the OSU Center for Health Systems Innovation, joined forces with faculty engineers from the University of Louisville to earn a share of a $1.5 million grant from the National Science Foundation. The goal was to develop and evaluate AI technologies that allowed robots to do routine patient-care tasks to alleviate stress during the nation’s nursing shortage. The Association of American Medical Colleges has warned about the possible shortage of more than 100,000 nurses by 2030.
Led by the grant’s principal investigator, the University of Louisville’s Dr. Dan Popa, the group developed ARNA, an adaptive robotic nursing assistant that was put to work at the Louisville School of Nursing. ARNA weighs about 500 pounds and utilizes cameras and lidar, a remote sensing method that uses light waves to examine terrain and objects, to navigate patient rooms and hospital hallways while helping nurses carry out tasks quickly and safely.
Edwards sees ARNA as a perfect example of how technology can help preserve and even create new jobs while solving problems in the workplace.
“We’re not trying to replace nurses. We’re trying to fill the nursing shortage and help our nurses," he said.
Some industries are better prepared for this new wave of technology than others. Robots are nothing new to manufacturing and logistics, but AI represents the next frontier for all businesses. Edwards and his team are hoping to anticipate some of the unintended consequences that might arise, and he thinks human bias could alter the information and interactions between humans and AI.
ChatGPT, an AI large language model (LLM) developed by OpenAI and launched in November 2022, essentially scrapes the internet to answer any question posed to it in a human-like way. It has the ability to write a joke, compose an email or even write a novel in a fraction of a second, and with every query the program learns. However, because ChatGPT is essentially reading the internet, it can give out biased or false data to the extent it runs across it during its searches.
In the future, it’s not hard to imagine an AI program assisting companies with human-resource tasks like employee recruitment and performance evaluations. Research shows that human bias exists in many HR systems based on gender, race and other considerations. So, to the extent that a company uses its own database to feed into the AI system, that bias in the database is going to be manifested in whatever outcome the AI has.
“If you’re using an algorithm to predict who to hire for a job or who to promote, bias is going to be built right into that AI,” Edwards said. “For example, women dominate the nursing field, so that’s going to be female-heavy bias in those algorithms. Males are more prevalent in engineering, so there’ll be a little bit more bias in some of that. So, for instance, if you’re building a robot in manufacturing, a field that’s dominated by men, the AI may not consider or compensate for women.”
The way to overcome these biases, Edwards said, is to teach the AI to decipher information better, which is certainly possible for a technology capable of learning. But, once again, the key to implementation is human intentionality and a laser-like focus on the goal of moving the technology forward.
“We cannot just sit and wait for somebody else to do it — we have to lead,” Delen said. “This is one of those projects that will put us at the forefront of leading the world into the next generation. We want to produce industry 5.0 type of manufacturing systems. Not just robots, but humans, robots and AI all bundled together in an optimal manner to create outputs that could not be created otherwise.”
These groundbreaking technologies won’t reach their full potential without researchers and scientists mapping out the future, finding ways to deliberately weave the technology and people together in safe and innovative ways.
OSU, with its modern land-grant mission, is at the forefront of these conversations. Put simply, OSU’s goal is to raise successive generations of servant-leaders who engage as vital members of their communities, to bring research and new knowledge to bear to prepare students for the world they will enter and to extend critical knowledge and expertise to meet society’s most pressing problems.
“I wouldn’t be able to do this type of work if I weren’t at a land-grant institution, a Research One institution, like Oklahoma State,” Edwards said. “We have a lot of support for this research, from former OSU President Burns Hargis to the current president, Dr. Kayse Shrum, and even here at Spears Business with prior Dean Ken Eastman and current Dean James Payne. The Power of Personal is definitely at work in this research.”