Changing the Dynamic
Thursday, November 5, 2015
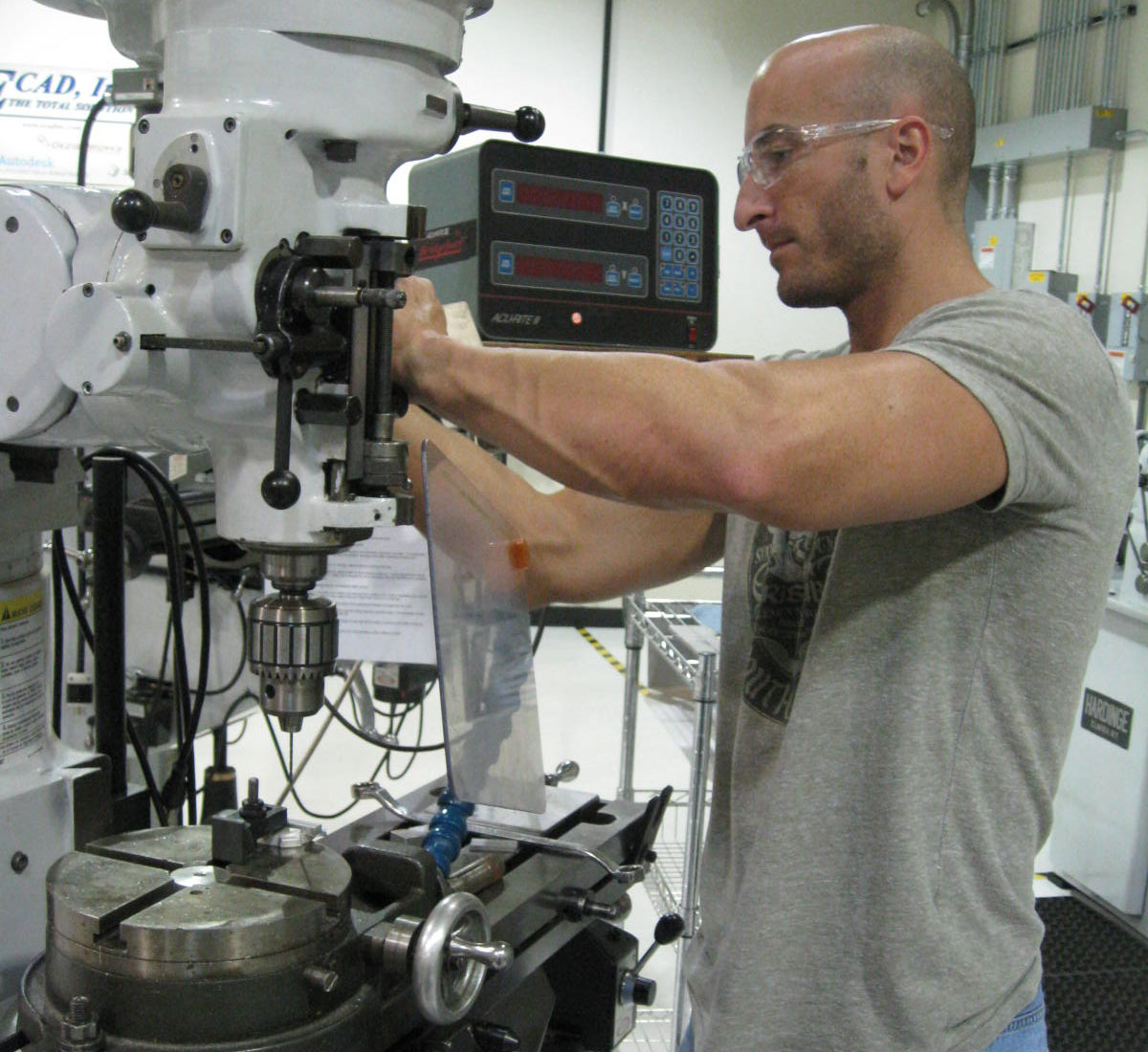
A unique hands-on facility at Oklahoma State University is pioneering a new avenue in engineering.
Under the direction of associate professor Warren Lewis and the guidance of coordinator Jeremy Crocker, the Mechanical Engineering Technology Lab (FabLab) in the College of Engineering, Architecture and Technology has grown to a fully functional engineering lab from a humble beginning with donated equipment in 2006. The lab was developed for a hands-on undergraduate education experience. Its growing success has increased OSU’s industrial partnerships as well as expanded the student educational resources available.
The lab gets students involved while meeting and exceeding safety standards in the industry. Faculty and staff are focused on providing students an opportunity to learn by safely and efficiently educating them on equipment and technologies.
“We don’t need a textbook; we are changing the whole dynamic,” Lewis says. “In the beginning, we give students small projects and then grow to bigger projects with more successes and potential failures to learn from.”
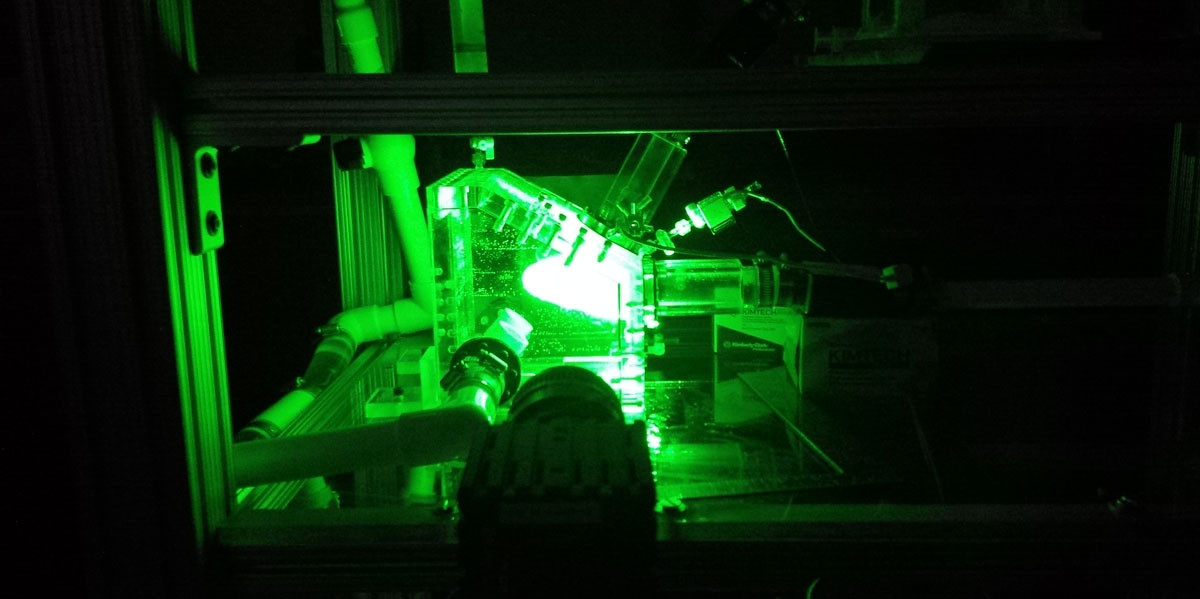
The lab gives intern engineers – undergraduate engineering students hired by the FabLab – a chance to make parts and see the design process from concept to reality through projects contracted by industrial partners and researchers.
“Depending on the intern’s work experience, it takes approximately one to two years to get the interns ready for a major project,” Crocker says. “We gradually step them through various capabilities of the lab while simultaneously exposing them to the various logistical aspects of a full project, until we think they are ready to be tasked with a real external project with real dollars attached to it.”
A diastolic heart chamber was a recent project at the FabLab. The heart chamber replicates the fluid dynamics of a single heart ventricle and uses lasers to track the fluid flow through a model of the left ventricle to study how the heart reacts to various heart diseases.
Arvind Santhanakrishnan, assistant professor of mechanical and aerospace engineering, is the innovator behind the diastolic heart chamber.
“My interest has been in creating a phantom model, which is basically a replica of whatever physiologic component you are interested in, which in this case is the left ventricle,” Santhanakrishnan says. “The left chamber of the heart pumps oxygen-rich blood to the rest of your body, and so the goal of this heart chamber is to basically create a phantom that can be seen through so that we can actually have a formable heart models that matched with the anatomical geometry and that can actually move similar to how the heart pumps. This way we can study what happens to the flow inside the heart when affected by different heart diseases.”
Santhanakrishnan needed a solution-driven design guided by the cost. There was a need for local resources, complex equipment and quick turn-around for the design, which is where the FabLab came in.
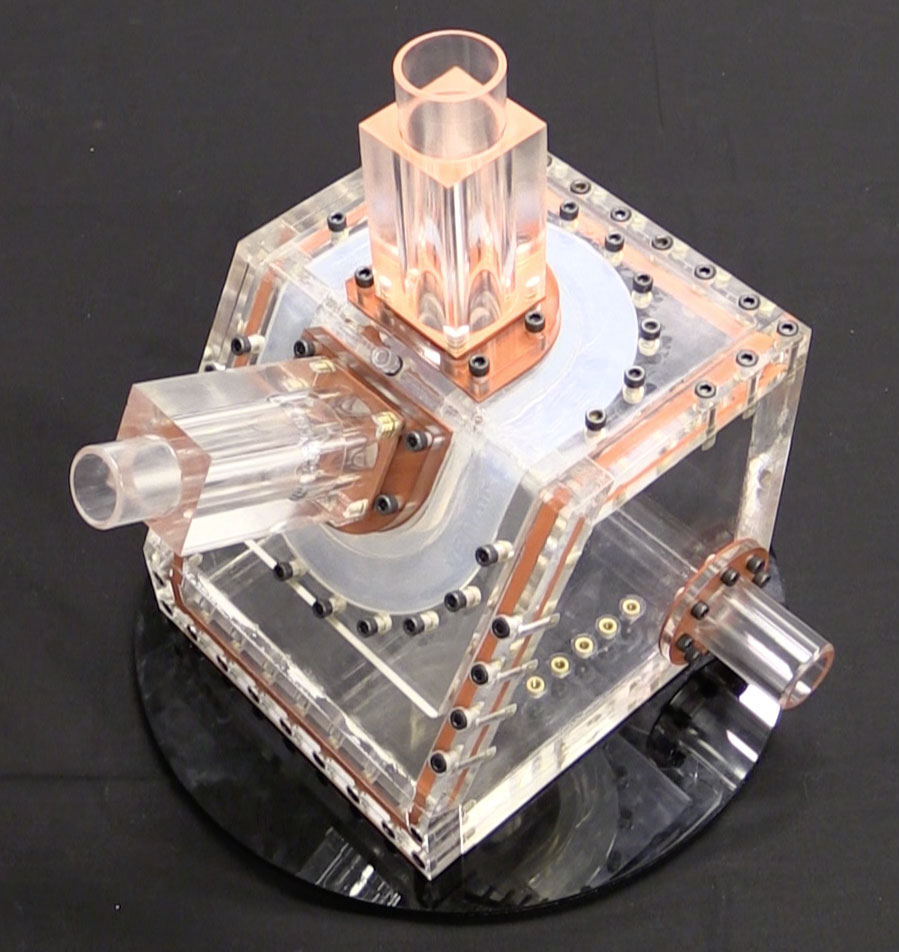
Larry Carden, a graduate intern of the FabLab, was in charge of the fabrication and manufacturing of the heart chamber.
Today, Carden is a systems engineer at Boeing Defense, Space and Security in Oklahoma City. At the lab, he gained engineering experience. Interns also work as lab assistants for the classes at the FabLab. As a lab assistant, Carden developed a deeper understanding of the coursework covered in those labs.
“Because the diastolic heart chamber was a project where I was able to experience the importance of design requirements and customer needs, it allowed me to ‘hit the ground running’ when I started my job after graduation,” Carden says. “Overall, it taught me a lot about managing all aspects of a project.”
There were continuous improvements to the project with design reviews and meetings with Lewis, Crocker and Santhanakrishnan. Carden determined costs and regulations and acquired the required documentation to proceed, which is another aspect that mimics industry.
“For any project, you should be prepared to have design changes develop,” Carden says. “It is important to keep this in mind while designing so that changes can be made efficiently. It sums up to staying flexible and keeping open communication with your customer to allow for quick solutions when problems arise.”