A Brighter Future
Friday, November 1, 2019
An OSU partnership sheds light on an industry problem
A lumen and the LUMEN are very different things. One is a measurement of light, while the other serves as a symbol of a brighter future for the oil and gas industry.
The LUMEN system is the future of methane monitoring, born from a collaboration involving Oklahoma State University’s Unmanned Systems Research Institute (USRI), its School of Mechanical and Aerospace Engineering (MAE) and the Baker Hughes Energy Innovation Center of North America in Oklahoma City. LUMEN is a technology that is expected to lead the oil and gas industry toward a greener future.
Defining LUMEN
The LUMEN system is a sensor network comprised of ground and air systems that can be used to pinpoint the location of a methane leak, as well as determine its severity in any number of oil and gas industry applications.
Why methane? Methane is the second-highest greenhouse gas emitted, behind only carbon dioxide, but since methane is 25 times more potent in trapping greenhouse heat, it is much worse for the climate. However, methane is also the most abundant gas used in natural gas-burning applications, because it’s abundant, cheap and produces less carbon dioxide than other fossil fuels.
The oil and gas industry adheres to strict standards for methane emissions because of its negative effects on the atmosphere. Also, in most cases, any methane leak represents a loss of revenue for the company.
This is where the LUMEN system’s application can save a company time, money and minimize their environmental impact.
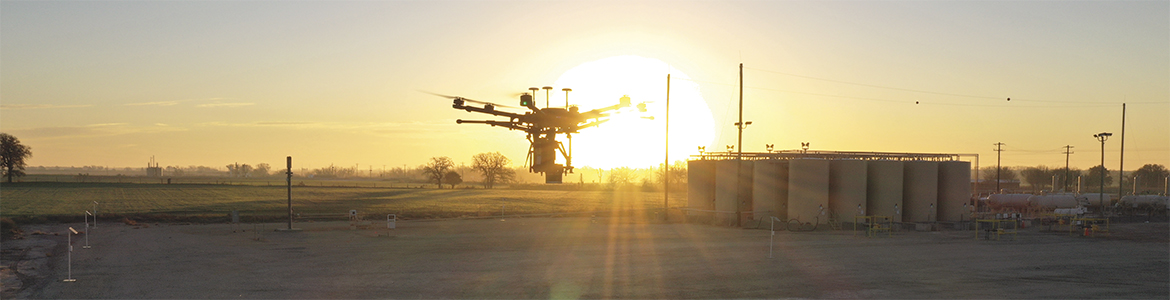
How it works
Envision a well pad that is acres in size with a pumping station that has a network of pipes and hinge points where methane leaks can occur.
The LUMEN system has a set of ground sensors set along the perimeter of the pad that would send an alert to the control system if methane is detected.
Once this alert is triggered, a team launches the aerial unit and scans the pumping station looking for leaks directed by a predictive algorithm utilizing machine learning. Once the leak is found, the aerial unit sends real-time data to the control system, giving the location and the severity of the detected leak. Simultaneously, the system uses the ground measurements to help localize the leak using advanced mathematical models.
The company addresses and solves the issue, adhering to methane emission regulations and preventing further losses. This process is completed in minutes vs. the multiple teams of people and days it would otherwise take.
LUMEN's Beginning
“The LUMEN project’s beginning was a bit serendipitous,” said Dr. Jamey Jacob, the director of USRI.
Jacob and his team were already working on aerial gas sensing technology for a U.S. Department of Energy project. When General Electric announced its plans for the Oil and Gas Technology Center in Oklahoma City, Jacob presented some projects that his team was working on when GE took notice of their current greenhouse gas detection, unmanned aircraft system.
The decision was made to build on this technology and focus on methane emission detection using an aerial vehicle, giving birth to LUMEN Sky. The initial idea focused on using commercial drones with sensor technology integration. Jacob and his team did so, on several different vehicles to prove the efficiency of the idea.
That led to the current combination of a hexacopter and its integrated sensor system. The extrapolation took almost three years and hundreds of test flights.
The integration of the sensor and its control system was built from scratch and went through several iterations of its own.
“It started with a handheld laser detector that transmitted to a small computer onboard and then would report the data to GE,” said OSU’s Dane Johnson, lead engineer for LUMEN Air. “It grew into an onboard computing system that could control the aircraft, as well as record the data from the methane detector, while receiving input from a LIDAR sensor (so they could map the oil pad as they flew overhead), and receive infrared camera data,” Johnson said.
The first prototype of LUMEN Air flew a predetermined flight path while recording and reporting data from a methane detector. That grew into a custom onboard computing system developed by OSU that could alter the flight path of the vehicle once methane was detected, then map the location and severity of the leak.
How do you keep all of this sensitive equipment safe and operable while attached to a vehicle that is 30 feet in the air? The answer is a unique mounting and containment structure of carbon plating and tubing. The mounting system needed to be “oilfield proof,” meaning “it could withstand 100-degree heat, sand, dirt, snow and simply the day-to-day wear and tear of oilfield usage,” Johnson said.
The LUMEN Terrain ground sensor was developed in conjunction with LUMEN Sky; it’s an accurate methane emission detection system that continuously and autonomously searches for methane leaks. The ground-sensing network delivers real-time quantification and notification of methane emissions.
All the data
The sensing technology was created to collect copious amounts of data and deliver it in real time to a monitoring station that could then dispatch a team to deal with a pinpointed methane leak.
“Any sensor data goes only as far as how you interpret it,” said MAE faculty member Dr. Balaji Jayaraman, the principal investigator and OSU lead for the LUMEN Predictive Analytics Technology for both LUMEN Sky and LUMEN Terrain methane-sensing efforts pursued by BHGE.
Most science focuses on predicting the effect of a known cause. Jayaraman and his team had to solve the inverse problem — measure the effect and predict the cause. This required the team to develop advanced modeling and simulation algorithms that went above and beyond the current tools available and provide a completely new approach for plume source localization and quantification.
“We think this approach could be a game changer and provide significantly improved prediction accuracy,” Jayaraman said.
The analytics system in use today is the second iteration of the software that will evolve as Jayaraman and his team continue to refine and improve the predictive analytics capabilities.
LUMEN's future
The overall inception, development and subsequent rollout of the LUMEN system took hundreds of tests, multiple iterations of every aspect and years of hard work from groups of both OSU and BHGE engineers.
However, the experience and knowledge gained through the partnership has been invaluable to all involved. “Working on this system has meant a ton to me,” Johnson said. “The wealth of knowledge I’ve gained from this project is great.”
Jayaraman echoes that sentiment: “I am happy for the opportunity to marry advanced predictive technology with cutting edge sensing infrastructure to address a complex problem with significant environmental and industrial implications. We are thankful to BHGE for the support and opportunity to collaborate with the excellent team at the Energy Innovation Center in Oklahoma City.”
Jacob envisions the use of swarm technology to further improve the efficiency of LUMEN Sky, as well as the possible implementation of fixed-wing vehicles to serve and scan pipelines that require much longer distances. The OSU team is developing and testing both aspects of these technologies at the OSU Unmanned Aircraft Flight Station, which recently received FAA permission to fly swarm aircraft beyond the visual line of sight. This testing will form the baseline for future developments.
LUMEN is poised to address a growing issue, not only in the oil and gas industry, but worldwide and usher in a brighter, greener future.