Every Drop Counts
Friday, November 1, 2019
Pankaj Sarin hopes to change the world through water treatment
After completing his doctorate in 2002 at the University of Illinois, Dr. Pankaj Sarin made a decision that would lead him toward changing the world, one drop of water at a time.
A Novel Beginning
Sarin attended the University of Illinois at Urbana Champaign for his doctorate program because of its prestigious material science program. His undergraduate degree in ceramics engineering came from Banaras Hindu University in India. Upon getting his Ph.D., he decided to focus his research on finding a new way to process ceramic membranes for water treatment applications.
These membranes serve as a filter, trapping harmful bacteria and chemicals as water passes through them. Most membranes today use organic or polymeric materials. However, Sarin and his graduate student at the time set out to create a new, less expensive ceramic membrane of readily available materials.
Ceramics are not readily used for water treatment membranes because of the high energy cost in processing the membranes themselves. The production temperature of a ceramic membrane runs between 1,000-1,500 degrees Celsius. However, Sarin believed that using a different approach could lower that production temperature to 80-100 degrees Celsius, substantially lowering the cost of the ceramic membranes.
Using more readily available natural materials and less energy for production make Sarin’s idea of a ceramic membrane very enticing. Also, ceramic membranes have a longer lifespan than other membrane materials, which would make the ceramic membranes more cost-effective.
In 2007, Sarin initiated his work on the project with graduate students at Illinois, but a lack of resources put the project on indefinite hold.
The Fork in the Road
Sarin continued his research in other areas of material science while waiting to restart his ceramic membranes project again.
Meanwhile, Dr. Raj Singh, director of the Energy Technologies program and Williams Chair Professor at the Helmerich Research Center at OSU-Tulsa, was working to start a material science program at OSU-Tulsa. His and Sarin’s paths had crossed at conferences and workshops, and Singh kept up with Sarin’s work.
He reached out to Sarin and asked if he would be interested in moving to Tulsa to be part of the foundation for the material science program. Sarin was intrigued, but he had never been to Oklahoma, let alone thought of moving there.
He sought advice on the opportunity. “The answers were very black and white,” Sarin
said. “People either thought I was crazy for even entertaining the idea or told me
that moving to Tulsa would be the best decision of my life.”
He took a leap of faith and accepted Singh’s offer.
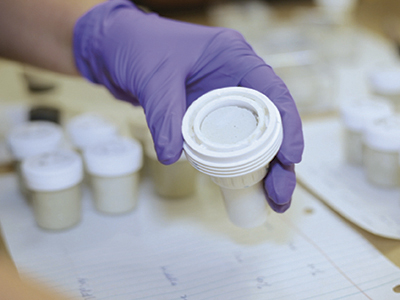
An idea reborn
Soon after Sarin joined the OSU-Tulsa team in 2013, he found the chance to rekindle
his work on ceramic membranes.
A researcher would generally take three to five years to find and refine the essence
of a problem that requires research. However, an oil and gas company walked in the
door and presented a problem to Sarin, saving him the time.
“That’s the great thing about OSU and the Helmerich Research Center: People come to us and ask us to solve their problems,” he said.
The problem was what to do with excess chemicals in produced water from the oil and gas extraction process. Sarin knew the best way to address the problem would be to better filter the chemicals out of the produced water. Of course, Sarin had been researching that very idea a few years prior.
Couple that coincidence with the addition of a graduate student who came to Sarin looking for a challenge, and the research into producing a new, more cost-efficient ceramic membrane was rekindled.
A work in progress
Sarin and his team of colleagues and graduate assistants have made progress toward a working prototype. The most recent membrane construction is 1 millimeter thick (roughly the thickness of a quarter), still much too thick to be efficient in its duties. The ideal membrane would be somewhere between 10-100 microns (the width of most human hairs), which would allow more water to flow through the membrane while retaining its structural integrity and maintaining an optimum level of filtration performance.
However, problems remain with constructing the membrane as well as developing a structure to hold a membrane that is too thin to see with the naked eye.
Sarin hopes that within the next year, he and his team can secure additional funding for developing the membrane and its containing structure. He is working on grant proposals that, if awarded, would bolster his overall funding for the project to approximately $2 million.
Five years from now, Sarin hopes that one of his students will have a startup company producing these ceramic membranes and supplying them to oil and gas companies around the world.
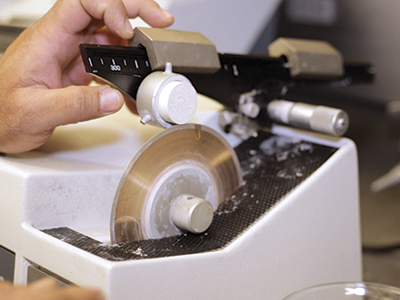
Myriad applications
Sarin also has his sights set on a more important problem that his new ceramic membranes would be ideal for solving: the scarcity of drinking water. The immediate application for the membranes is in the oil and gas industry, but the possibilities for their application is much broader.
The scarcity of drinking water faces countries around the world. One solution would be to desalinate seawater. Sarin believes that the new membranes would be a valuable asset toward that end.
“We’re working on a project that would be 10 times harder than the desalination of seawater,” Sarin said in describing his work with the oil and gas industry. While the actual desalination of seawater would be easier, much work would be required in the transition, as the restrictions on drinking water are very stringent.
However, it is still on Sarin’s radar. “I have contacts in the world of water treatment from my time at Illinois,” Sarin said, adding he hopes to move into seawater desalination within 10 years.
From pursuing the idea of creating a new ceramic membrane to taking the unknown side of the fork in the road to the many more choices in the future, Sarin doesn’t shy away from challenges or struggle with whether he made the right choices.
“Decisions are easy to make — determining whether they were right requires a lot of effort.”